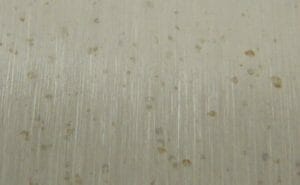
One of the first things customers usually say when entering our trade show stall is “Wow, the stainless steel looks great!” We do go to great lengths to make sure things look good, but most of our effort is spent ensuring that our Stainless Steel NEMA 4X products meet the functional anti-corrosive needs of our customers. Equipment used in the food/beverage, pharmaceutical, and chemical industries must be highly resistant to water, cleaning/sterilization, and other industrial chemicals.
Stainless Steel Materials Choice
When considering materials to use in the fabrication of enclosures and mounting fixtures for industrial monitors and keyboards, stainless steel is often the material of choice, especially when the device is exposed to water and cleaning agents. But not all stainless steel is created equal and there is more to it than meets the eye – literally. The first decision point is whether to use 304 or 316 grade stainless.
Grade 304 (also called standard “18/8” stainless: 18% chromium, 8% nickel, the rest iron) is extremely versatile and is extremely common in anti-corrosive applications. It is available in a variety of forms and finishes and has great forming and welding characteristics.
Due to its lower cost, 304 is much more common than 316 for industrial use and is standard on all of our products. This meets the needs of the vast majority of industrial users, but when 316 is required it is an easy customization we can make to any of our NEMA 4X stainless steel products. We have made 316 versions of many of our industrial touch screens, keyboards, and mounting options.
Stainless Steel Preparation and Tooling
Beyond selection of the grade of stainless, there is another very important factor that affects the final performance of any grade of stainless product. Improper surface preparation can make even the best grades of stainless steel appear to be rusting. If the proper care is not taken, iron from tools that were used on non-stainless grades of steel can impregnate the surface of stainless steel. If the surface of stainless steel becomes “contaminated” with iron, it will develop corrosion stains from iron oxide that will make even the best stainless steel appear to be corroding. The original contamination cannot be seen with the naked eye or any basic magnification, and it may take several weeks for the corrosion of the surface iron to become visible.
The adage “an ounce of prevention is worth a pound of cure” applies in this issue. Special care can be taken by the fabricator to ensure tools and sanding belts used on stainless steel are not used on any other metals. We maintain separate tooling in our workshops to ensure that this contamination does not take place. We also work closely with outside metal fabrication shops to ensure that this precaution is taken at all stages of our products’ production.